Warehouse Management Global Setup
We have deprecated the Take an
Order Interface option on the Global Setup-> Add-ons menu. The option
Warehouse Management System will replace the old option. This new application
is available:
1. Enable Warehouse Management System: This option allows the user to
enable the Warehouse Management System.
2. Staging Batch ID: A sequential
Staging Batch ID that will be used when staging batches are created.
3. Allow Staging Batches Verification
to Complete If Under Verified? (N=No, A=Allowed with warning, P=Allowed with
Password -- default is A)
4. Under Verified Order Password: If a user exits when processing a staging
batch and the batch is not fully verified, the following will happen based on
the setting:
N – The batch will be marked as partially
verified.
A – The user will be presented with a warning
screen asking if he/she is finished processing the batch. If the user answers Y, the
batch will be marked as verified. If the user answers N, the batch will be marked as
partially verified. Default is N.
P – The user will be presented with the same
warning screen as the A setting but if he/she answers Y, the user will be asked to
enter a password to proceed.
5. Show Unassigned Staging
Batch? Y/N: If the WMS Global Setup Flag to show
unassigned staging batches is set to No, all records that
have not been assigned to a user will be filtered out automatically and the
user will only see the batches that have been pre-assigned to him/her. If the WMS
Global Setup Flag to show unassigned staging batches is
set to Y, staging batches that are unassigned are also shown.
6. Show Unassigned Transfer
Batch? Y/N: If the WMS Global Setup Flag to show unassigned
replenishment batches is set to No, all records that have
not been assigned to a user will be filtered out automatically and the user
will only see the batches that have been pre-assigned to him/her. If the WMS
Global Setup Flag to show unassigned replenishment batches is set to Yes, staging batches that are unassigned are also shown.
7. Staging/Bin Transfer Field Option 1
8. Staging/Bin Transfer Field Option 2
These
options will allow the user to choose the fields that are shown in the UPC and
Mfg Item spaces on the Staging Verification screen in Elliott. The choices will include Item Desc (option 1
only – if chosen, option 2 will be used to accommodate the size of the item
description field), Item Note 1,
Item Note
2,
Item Note
3,
Item Note
4,
Item Note
5,
Prod Cat Desc, Volume, Weight, Ext Volume, Ext Weight.
9. Allow Changes To Attrib Qtys
in I/M Transfer?: This option will allow the user
to choose whether or not warehouse personnel can change the Target Qty or the Threshold
Qty on the PICKBIN attribute when in the Bin Replenishment application. The
default value is N.
10. Count Scan Zone 2 Field 1
11. Count Scan Zone 2 Field 2
12. Count Scan Zone 4 Field
13. Count Scan Zone 5 Field
These options will allow the
user to choose the fields that are shown on the WMS Count Detail Screen.
Fields 10 and 11 have the following options:
- 1=
Item Note
1
- 2=
Item Note
2
- 3=
Item Note
3
- 4=
Item Note
4
- 5=
Item Note
5
- I=Item Desc
- P=Prod Cat Desc
- V=Volume
- W=Weight
- X=Ext Volume
- Z=Ext Weight
Fields 12 and 13 have the following options:
- Q=Qty On Hand
- T=Total Qty
- A=Qty Allocated
- U=User
- D=Date/Time
14. Sort Bin Replenishment By: This option will allow the user
to choose whether he/she would like the WMS Transfer screen for a non multi-bin
replenishment batch to sort by the To Bin or the From Bin. (This option is obsolete. The WMS is only supported in a multi-bin environment.)
15. Cancel Pick Ticket Override
Password: This option will allow the user
to choose whether or not the ability to cancel a picking ticket that has
been processed through a staging batch can be cancelled. If the password is entered,
the user must enter the password to cancel the pick ticket.
16. Show Warning Window for
Wrong Item/Over Pick?: This option will
allow the user to choose whether or not a warning window will pop up in the case of a miss
scan. This can be helpful for pickers because it will force them to see that
there was an error and type DONE before moving on to rescan the proper item.
17.
Wave File For Overpick?
18.
Wave File for Wrong Item?
19.
Wave File For Confirm?
20
Wave File for Alert?
These
options will allow the user to configure the sounds that can be heard during
the course of processing a staging batch.
21.
Staging Ver Serial Display Area For I Type: This
option will allow the user to control where the serial numbers will be
displayed during staging verification of an “I” type order.
22.
Use Paperless Transfer Tickets: This
option will allow the user to choose whether transfer batches should be marked as
printed and processed electronically or whether they will be printed on paper.
23.
Allow ShipVer/Bill Batches Not Stage Verif?: This
option will allow the user to choose whether staging batches that have been
created but not processed through staging verification can be processed through
shipping verification or standard billing.
24.
Transfer Batch Serial Display Area: This
option will allow the user to control where the serial numbers will be
displayed during processing of I/M Receiving, PO Receiving and Production Order
Processing production reporting transfer batches.
25.
Show Serial No. In Shipping Ver for I Type
26.
Shipping Ver Serial Display Area for I Type
These options
will allow the user to choose whether or not the serial numbers associated with
an “I” type order will be displayed individually in Shipping Verification. If
this option is set to Y, the user will also be able to control where the serial
numbers will be displayed during Shipping Verification.
27. Min Serial No. Scan Required Bin To Bin Tsf?: This option lets the user set up the minimum number of serial number scans when performing a Simple Bin Transfer.
28. Use Ser# Alloc When Assign Bin in Stg Ver?: This option lets the user choose whether or not Staging Verification should take the serial number quantity allocated into consideration when suggesting bins using the F8 function key. If this option is set to Yes, the program will subtract the serial quantity allocated from the bin quantity available. Setting this option may slow processing when using the F8 key in Staging Verification, but the assignment is more accurate.
29. Put Away Field 1
30. Put Away Field 2
31. Put Away Field 3
These options let the user choose which fields are displayed on the Put Away Processing Item List screen.
For fields 1 and 2, the choices will include Item Desc (option 1 only – if chosen, option 2 will be used to accommodate the size of the item description field),
Item Note
1,
Item Note 2,
Item Note
3,
Item Note
4,
Item Note
5, Batch Number, Item Description, and Reference number. For a PO receiving the reference number is the PO number. For an inventory management receipt, the reference number is the item number. For a production parent reporting, the reference number is the production order number.
For Put Away Field 3 the choices include receiving date, extended weight, and quantity on hand.
32. Release Incomplete Put Away For Processing?
This option lets the user specify if the put away batch that is created during the put away process should be released for other users to work on if the initial user escapes out of the put away process before it is complete. If the option is set to N, the put away stays intact and assigned to the initial user. If Y, the items that are remaining are split off to a new unassigned receiving batch and released for other users to process. The items put away are posted.
33. Require PICKBIN Attrib Exist Before Put Away?
This option lets the user specify if the PICKBIN attribute must exist for the item before allowing it to be processed through Put Away Processing. Valid options are Y=Yes, N=No or P=Yes with Password override. If P is chosen, the user will be prompted to setup a password to override the requirement.
34. Use Blank Putaway Bin?
This option lets the user specify if the Put Away Processing applicat should default to a blank bin for the put away process. Y means only items not currently stocked will default to a blank bin. A means all items will default to a blank bin forcing warehouse personnel to provide the receiving bin. N means the bin will default to the primary bin in the item master or inventory location file.
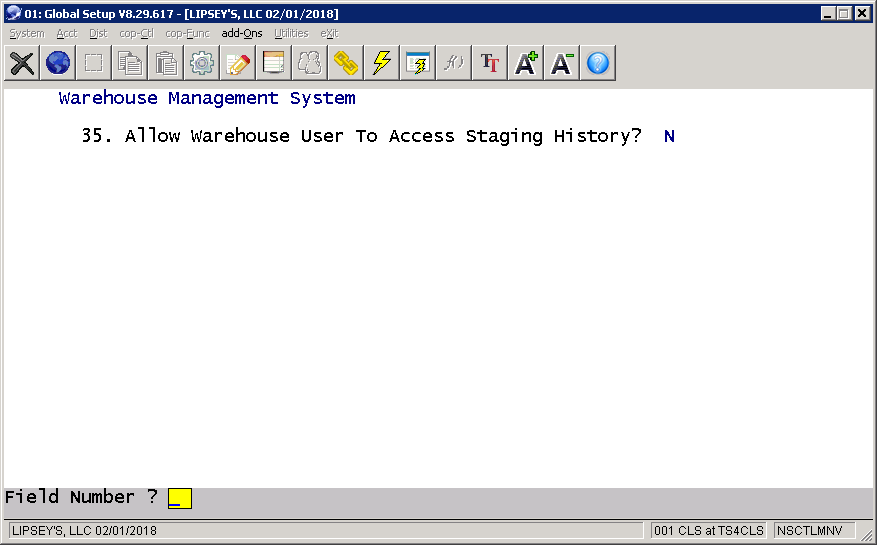
35. Allow Warehouse User To Access Staging History - The default value is Y. If set to N and the the user type specified in Password Setup for the user is set to "W" for warehouse user, the user will not be able to access the Staging Batch History option (F3) from the Pick Order Processing or the Pick Order Inquiry screens.
Pick/Pack Ticket/Ship Label Global Setup
The following options were added to support the Warehouse Management System.
33. Print Staging Summary By Bin/Item Or Order?
Options include B=Bin/Item Sum. Only, O=Detail
with Order Sum., and D=Detail with Bin/Item Sum. The default value is
"O" since that is the current behavior. The staging slip program will
use this flag to determine the format of the summary page and whether the order
detail will print.
34. Staging Summary Field Option 1
35. Staging Summary Field Option 2
These options have been added to the COP Global Setup to allow the user to choose the fields that
print in the UPC and Mfg Item spaces if the user chooses to print the summary
by Bin/Item instead of by Order. The
choices will include
Item Note
1,
Item Note
2,
Item Note
3,
Item Note
4,
Item Note
5,
Prod Cat Desc, Volume, Weight, Ext Volume, and Ext Weight. Any field chosen that is
over 15 characters in length will be truncated.
These fields will
also be used to control the user-defined fields that are displayed in the
Staging Verification application.
40. Print Order Summary on
Staging Slip?
Default Is No. If this
option is set to Yes, a list of orders on the staging batch chosen will be
printed as the last summary section. If this option is not to N, the order
summary will not print.
Shipping Verification Global Setup Changes
The following options were added to Global Setup-> Add-Ons->Shipping Verification to support the Warehouse Management System:
52. Shipping Verification Field Option 1
53. Shipping Verification Field Option 2
These options will allow the user to choose
the fields that are shown in the UPC and Mfg Item spaces on the Shipment
Verification screen in Elliott when the Warehouse Management System is in use. The choices will include Item Desc (option 1
only – if chosen, option 2 will be used to accommodate the size of the item
description field),
Item Note
1,
Item Note
,
Item Note 3,
Item Note
4,
Item Note
5,
Prod Cat Desc, Volume, Weight, Ext Volume, and Ext Weight. Any field chosen that is
over 15 characters in length will be truncated.
54. Auto Pop Up Note For This
Note Type
This option will allow the user to choose whether he/she would like notes
to pop up after an order is selected during shipping verification. If the field
is blank, no notes will pop up. If the note type is provided, the program will
look for that note type for that order. If it exists, the notes application
will pop up so the user can choose to view the notes associated with that
order.
55. Allow Verification For Cust
On Credit Hold?
This option will allow the user to choose whether or not to allow
Shipping Verification for orders on credit hold. If the answer is N, the user
will be prompted with an error message if the customer is on credit hold and
the order cannot be verified.
56. Show To Ship and Confirm
Qtys Side By Side
This option will allow for backward compatibility with the old
screen layout.
57. Use TTS During Shipping Verification?
This option allows the user to turn off TTS during Shipping Verification. This should be set to N if users are experiencing page locks on the Serial/Lot Master file. The default is Y.
58. Allow Re-Verify WMS Ord By Diff User?
This option allows users to choose whether or not a user can re-verify an order that was processed through Shipping Verification by someone else. If this option is set to Y, the program will prompt for an override password.
I/M Global Setup
The following options were added to I/M Global Setup to support the Warehouse Management System:
8. Validate Pick Seq Against
Bin Master File?
9. Allow Blank Pick Seq?
These options will allow users to validate the picking seq/primary bin number in
the Item Master and Inventory Location Control files against the Bin Master
file. The Allow Blank Pick Seq flag will allow the user to choose whether or
not blank pick seq/bin numbers are allowed.
10. Serial No. Change Log File Path & Name
This option allows users to specify the name of the log file that is generated when running
the Serial Number Correction Tool.
The following change was made to Order Header Global Setup to support the Warehouse Management System:
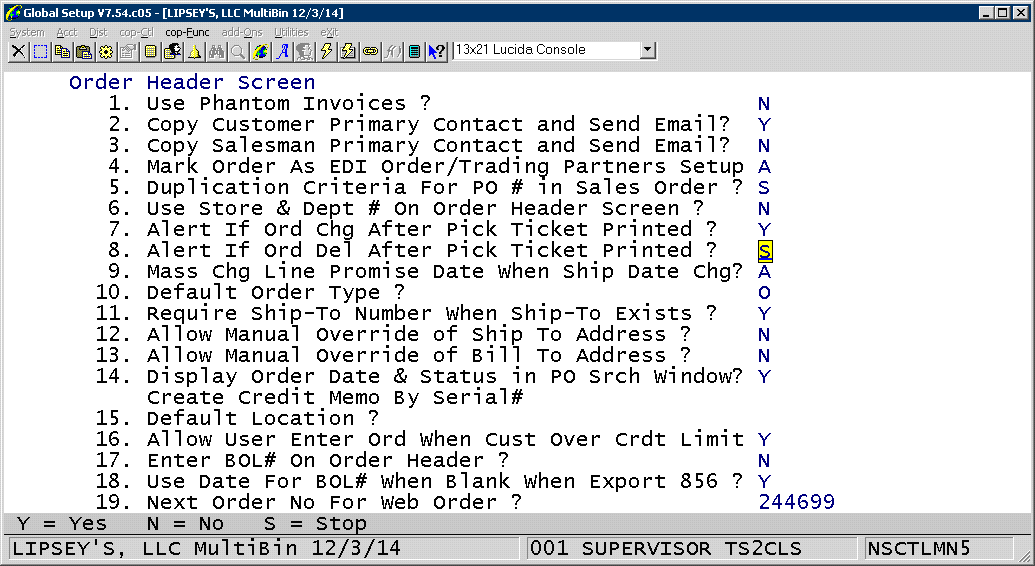
8. Alert If Ord Del After Pick Ticket Printed?
A new option of “S” has been added. This new option will stop the deletion of the
order if the picking ticket has been printed. The proper procedure to delete
the order will be to cancel the picking ticket before deleting the order. If
the order has already been staged, cancel the picking ticket. This will delete the WMS order from the
system and remove it from the assigned staging batch.
Inventory Transfer Control Global Setup
The following options were added to Inventory Transfer Control Global Setup to support the Warehouse Management System:
16. Default Restocking User ID to Blank?
17. Default Free Batch User ID to Blank?
18. Default PO Receiving User ID to Blank?
19. Default I/M Receipt User ID to Blank?
20. Default COP Shipping User ID to Blank?
21. Default BOMP Component User ID to Blank?
22. Default BOMP Parent User ID to Blank?
These options let the user decide whether the system defaults the assigned user ID on the transfer batch that is created is set to blank or to the user who ran the report.
Multi-Bin Global Setup
The following options were added to Multi-Bin Global Setup to support the Warehouse Management System:
27. Prompt Multi-Bin Info During Billing Selection?
This option lets the user choose if the user will be prompt during billing for the bin number if No Transfer Ticket or Staging Batch Processed (O), Always (A), or Never (N). If never is selected, the bin will default to the SHIP bin for the location. This option is only applicable if running multi-bin 1.0.
29.Default Bin For Returns
This option lets the user designate an RMA bin that will be used when inventory is returned from a customer. This one bin designation will be used for all warehouse locations.
30. Print Min Transfer Report Immed After Pick Tickets?
This option lets the user choose whether the user will be prompted with a question to print the Minimum Transfer Requirements Report immediately after pick tickets are printed. If the user prints the report, a transfer batch will not be created. Report is run for informational purposes only. No bin replenishment transfer batches will be created.
31. Use Priority Bin If There Is A Pick Bin?
This option lets the user choose whether only the pick bin should be used when printing pick tickets or transfer tickets. If this option is set to Yes, only the pick bin will be used on these documents if designated in the Item Master or Inventory Location Control files regardless of the quantity available at the pick bin. If a pick bin is not set up, the priority bins will be used. If this option is set to No, all stock bins will be considered for picking in priority order.
32. Force Inventory Transfer When Change Pick Bin?
This option lets the user choose whether changing an item’s primary bin through the Change Bin No./Pick Seq application will force the user to transfer all inventory in the old primary bin to the new primary bin.
33. WMS Put Away Bin
This option lets the user designate a bin that will be used when certain cancellation functions are performed in the system. For example, if a picking ticket is cancelled after a staging batch has been completed, the inventory will be transferred from the equipment bin to the put away bin.
34. Update Item/Inventory Location Primary Bin
This option lets the user choose whether or not the system will update the primary bin specified in the item master or location control file for an item. N is the default option. There are three options available:
D=Dynamically When Qtys Change - Anytime the a bin inventory record is created, updated or deleted, the system will determine if the primary bin needs to be changed. The following rules will be applied:
- If deleting a bin inventory record, the primary bin will only be changed if the bin number on the record being deleted matches the current primary bin for the item/inventory location.
- If changing a bin inventory record, the primary bin will only be changed if the bin number on the record being changed matches the current primary bin for the item/inventory location and the quantity available in the bin is less than or equal to zero.
- If adding a bin inventory record and the priority is in the priority range specified in Multi-Bin Global Setup, the system will check to see if the primary bin on the item/inventory location needs to be updated.
M=Manually Via Utility – This means that the primary bin will only be updated when running the new Reset Primary Bin Utility that is available. The utility is run from I/M-> Processing-> Serial/lot/bin Processing-> Bin-> Utility-> Reset Primary Bin.
N=No – This means that the user does not want to update the primary bin number dynamically or via the utility program. The pick bin must be set by hand for each item via the Change Bin No/Pick Seq or through Item File Maintenance or Location Control File Maintenance.
If the above flag is "D" or “M,” then a pop up window will allow users to set up a range of priority dates. This range of priority means the "picking bins" range. Entry of a zero priority for the starting priority means ALL priority dates are to be considered when dynamically resetting the primary bin.
35. Create Inventory Transfer For COP Tsf Orders
A value of Y will create a transfer batch when items are received in COP Transfer Receiving. Added Multi-Bin, Serial/Bin Cross Reference, and Transfer Batch support to COP Transfer Orders. Support is available for Transfer Order transfer batches in WMS Put Away Processing.
36. Consider Frozen Date When Delete Zero Qty Bins
Field defaults to Y. A value of N will cause bins with zero quantity on hand and zero quantity allocated to be deleted, regardless of the frozen quantity on hand or the I/M Control File freeze date.